Features of Tsuji Shiro's guitar
The guitar with amazing sound quality and bass
The secret to the bass is the thickness of the sound board
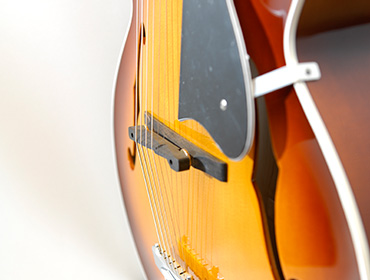
In a guitar, the vibration of the strings is transmitted to the sound board (front and back plates) and resonates with the body, causing the sound to resonate. The quality of the sound board is the decisive factor in the sound quality of the guitar. At first glance, a thin sound board seems to vibrate easily, but the sound becomes lighter.On the other hand, if the sound board is thick, the bass will come out firmly and the sound quality will be much better.
Shiro Tsuji paid attention to this characteristic and realized a heavy sound quality with thicker sound board and bass. It's easy to say and difficult to do. This is because a guitar with a thick sound board does not vibrate and the sound is less likely to resonate.
Why does the sound resonate even if the sound board is thick?
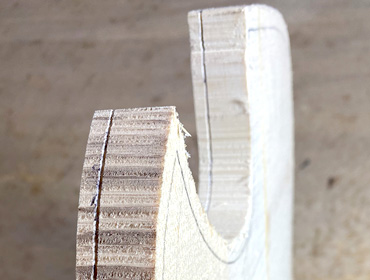
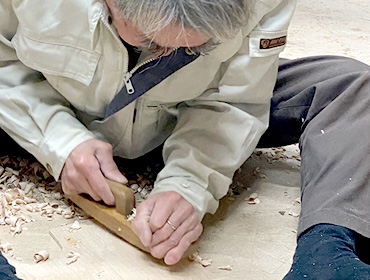
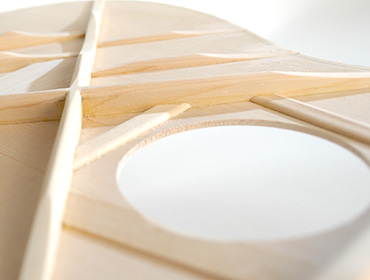
It is necessary to make the sound board thicker in order to make the structure sound the bass. However, if the sound board is thick, it will not vibrate and the sound will not be heard. We have solved this contradiction by using the semi-press method, material selection, and bracing.
Single plate structure
The sound board of mass-produced guitars mainly uses a board called "plywood", which is made by laminating a decorative material and a core material.
The feature is that the cost is low and it is hard. However, since plywood has vertical and horizontal streaks overlapped and pasted together, it hardly resonates when it becomes thicker.
On the other hand, our studio manufactures sound boards with a single plate. A single plate is a "single plate" and vibrates more flexibly than plywood. A single plate is suitable for making the bass sound.
Semi-press method and hand finishing
The center of the archtop guitar is raised like an arch. In the case of mass-produced products, the press method (all finished by machine) is common, but at our workshop, we finish by the semi-press method. The semi-press method is a method in which after forming a certain shape with a machine, the rest is manually adjusted and finished. A thick sound board does not sound with a mechanical finish. The power of craftsmen is indispensable.
Unique bracing adjustment
There is also a device to make the sound resonate in the bracing inside the sound board. Bracing is to prevent deformation of the body, but you can also improve the sound by devising the shape and arrangement.
At our workshop, we have created a unique bracing arrangement through repairs by leading manufacturers such as Martin and Gibson for more sounding bracing. This is one of the secrets of a guitar that sounds good even if the sound board is thick.
50 years of research and technology
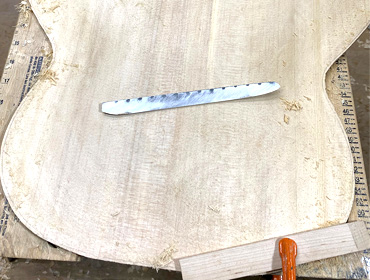
At our workshop, even ordinary guitars can achieve the same sound quality as high-end materials. For example, even Sitka spruce material can achieve the same sound quality as the finest Adirondack spruce material.
Good sound quality is determined by processing technology. Even if it is a general material, it will be much better if it is processed excellently. Obviously, if you use good materials, the sound quality will be even better.
At our workshop, we make the highest quality guitars with the technology cultivated through 50 years of research and trial and error.
What surprises professional musicians when played on this guitar is the performance such as "power," "flat response," and "playability," and the sound quality.
Every guitar has its own quirks. For example, a dead point where no sound is heard.Musicians take advantage of the good parts of the guitar, while supplementing dead points with techniques. However, our guitar has no dead points.
Handmade is one of the factors, but it is not the only one. Our guitar has a structure that sounds more bass than a normal guitar. The more bass sounds, the more powerful the sound changes. There's a clear reason why our guitars sound more bass than regular guitars. I will explain the point.